2014 das erste Hahnenmoos „Spektakel“ für Jürgen, Rene und mich. Schnell wurde uns klar das wir was Leistungsstärkeres brauchen ;-)…Da wir selber bauen möchten und der Bausatz im Rahmen unserer Budgets bleiben sollte, sind wir auf Rippin Top aufmerksam geworden.Roland L. schloss sich unserem vorhaben an und somit bestellten wir im September 4 Stk Pilatus.
Kurz vor Weihnachten standen 2 grosse Pakete vor der Haustür.
Weihnachten war gerettet 🙂
Andreas Safron
Baubeginn 31.01.2014
Da wir (Jürgen, René und meiner einer) noch unerfahren in diesem Gebiet sind, können wir auf die Hilfe von Roland L. und Roland O. (und natürlich auch alle anderen des Vereins 😉 ) zurückgreifen, die uns immer wieder Tips geben und auch beim Bau helfen.Die Steckung wird mittels 5min Epoxy angeheftet und in Folge mit eingedicktem 24Std. Harz im Rumpf fixiert.Der Rumpf wird zuerst innen mit Schleifpapier grob aufgeraut, damit das Harz besser haftet. Wir erstellen zuerst eine Schablone der Flächenrippe und markieren dann die Bohrlöcher am Rumpf. Die Schablone sollte vorne und oben gut passen. Mit kleinem Bohrer, bohren wir die Löcher vor und schleifen dann die Vorderen aus. Beim anzeichnen immer alles von vorne nach messen.Die Messingsteckung wird ebenfalls angeschliffen und alles mit Aceton gereinigt. Nun können wir mittels Kreuzlaser und Vermessen der Flächenenden zur Seitenflosse, die Steckungen vorsichtig anheften.Leider hab ich von dieser Aktion keine Fotos mehr :-(Nach dem austrocknen wird die Steckung mit 24 Std. Harz, Baumwollflocken und Thixotropiermittel fixiert damit das ganze nicht im Rumpf davon rinnt.Mit der Stirnlampe bewaffnet legen wir den Rumpf auf den Kopf, damit sich die Mumpe ordentlich reinstreichen lässt.
Die B4 soll auch Hang tauglich sein, somit werden ein paar Schwachstellen verstärkt. Vorne eine Lage Aramidgewebe mit Kohle rein und ein Spant der hoch bis zur Steckung reicht und mit dieser verbunden wird.Bei der Schwanzflosse wird eine Art Löffel eingeharzt, welcher den hinteren Teil des Rumpfes an der Seitenflosse verstärkt. Die Teile werden mit 80er Köper und eingedicktem (Baumwollflocken + Thrxotropiermittel) 24 Std. Harz zusätzlich verstärkt. Zusätzlich werden die Ecken an der Kabine verstärkt.Zuerst werden Vorlagen aus Karton und Sperrholz gefertigt. Spant und „Löffel“ wird dann aus 3mm Flugzeugsperrholz erstellt.
Nachdem die Spanten fertig sind, harzen wir das Aramidgewebe ein. Das Gewebe reicht von der Nase bis hinter die Radposition.Wie schon erwähnt soll die B4 auch am Hang genutzt werden und so haben wir (Rene und ich ) uns entschieden das Rad abnehmbar zu realisieren. Nur weiß ich noch nicht wie. Also wird beim Clubabend mal ein bisschen gezeichnet und diskutiert. Das Ergebnis sieht nun so aus das wir dass Rad von unten mit der Achse in Hartholz Klötze einlegen, und mit kleinen Abdeckungen fixieren. Schwer zu erklären einfach Bilder ansehen ;-). Die Raddurchmesser und Position hab ich von der Original B4 Daumen mal Pi errechnet. Also Loch raussdremmeln.Die Klötze haben wir dann an der richtigen Position mit doppelseitigem Klebeband fixiert damit der Spant angepasst werden kann.R vorne: 90mmR hinter: 30mm
Jetzt geht’s los mit der Harzerei 🙂 An einem gemeinsamen Abend, haben wir uns an das einharzen sowie an sonstige Kleinarbeiten gewagt 🙂 Hierzu haben wir wieder entsprechende Hilfe von Roland und Roland erhalten, sowie moralische Unterstützung von Kurt 😉 .. Also anschleifen, rein damit und noch mit Glasgewebe verstärkt. Das Seitenruder wurde gleich noch um 6mm gekürzt und auch gleich mit einen 3mm Bowdenzugrohr versehen. Mit 3mm Balsa eingehült und zum Schluss nochmal Balsa draufgeklebt. Das Ruder haben wir auch unten etwas schräger geschnitten damit bei den Landungen am Hang das Ruder nicht einen Schlag bekommt.Das Höhenruder haben wir vermessen und die Mittellinie angezeichnet.
Die Achsenführung wird mit dem Dremel eingefräst und das vordere Rad auf geraden Lauf kontrolliert. Anschließend die Achsenhalterungen mit Gewebe und Kohlerovings hergestellt.
Das hintere Rad wird angezeichnet und ausgeschnitten. Auch hier haben wir innen wieder 2 kleine Holzklötzchen als Lager verwendet. Allerdings wird beim hinteren Rad der Rumpf durchbohrt. Als Führung verwenden wir ein 3mm Messsingröhrchen und einen 2mm Stahl als Welle. Die Welle wird dann einfach mit Leim fixiert, so kann die Achse auch mal leicht getauscht werden. Eine Radhaube wird gleich mit ein geharzt, damit nicht das ganze Unkraut im Rumpf rumfliegt. Rene hat seine aus Balsa gemacht und ich aus Glasleinen und Kohlerovings.
Weiter geht\’s mit dem Höhenleitwerk.Eine neue Herausforderung da wir sowas auch noch nie gemacht haben. Anhand der vorher angezeichneten Mittellinie stechen wir mit Stecknadeln dieser entlang um herauszufinden wo der Sperrholz klotz liegt. Das vordere Loch wird zuerst gebohrt. Anschließend vermessen wir zu den Flügelenden und zur mitte des Rumpfes und bohren dann das zweite hintere Loch. Anschließend wird ein Sperrholz mit Einschlagmuttern in den Rumpf gehartzt. Das Servo wird von oben zugänglich gemacht und der hintere Teil wo das Ruderhorn einfährt mit Kohlerovings verstärkt. Die EWD wird auf 1,3 Grad eingestellt.
Jetzt wird das Ruder getrennt und verkastet. Servokabel werden eingelegt.
Nachdem das Höhenruder und die Anlenkung sitzt, können wir den Spant für das Seitenruder einharzen.Der Spant wird aus 4mm Balsa gebaut und verstärkt. Zusätzlich wird der Spant noch mit 40g Leinen belegt und schlussendlich mit Rovings eingeharzt. Das Seitenruder erhält die Schlitze für die GFK Teile. Die GFK teile werden mit dem Seitenruder eingeharzt für optimalen Sitz.
Das Seitenruder Servobrett wird in der Schlittenvariante gebaut. Mit einer Rändelschraube kann ich so die Seile der Anlenkung spannen. Insofern sie dann gleich lange sind 😉 Die Kollegen ohne Rad, verbauen ein Servobrett vor dem Hauptspant für Seite und Schleppkupplung. Die Schleppkupplung werde ich vorne mittig einbauen, weiß aber noch nicht wie 🙁 ..Danke Martin für den Tip mit dem Schlitten ;-)Hinter dem Servokasterl wird der Empfänger platziert.
Mit einer Schnurr am Rumpf entlang wird die ungefähre Position für den Auslass der Seile ermittelt. Ausschneiden, Auslass rein und die Position des Ruderhorns am Seitenruder mittels eines Lineals anzeichnen. Zuerst wird ein Muster des Ruderhorns erstellt und anschließend das GFK Teil. Naja schön ist es nicht aber selten und funktioniert.
Da uns der mitgelieferte Haubenrahmen nicht gefällt, haben wir uns entschlossen diesen mit einfachen Mitteln selber herzustellen. 5x20mm Kieferkeisten und 10mm Balsa schon ist der Rahmen fertig. Das ganze wird an den Rumpf angepasst (geschliffen).. Achtung beim schleifen an der vorderen Seite! Sonst passt der Winkel zur Haube nicht. Am besten die Haube grob vorschneiden und als Hilfe benutzen. Der Rahmen wird vorne mittels Stift fixiert und hinten mit Magneten.
Der Instrumentenpilz bzw. die Anordnung hab ich im Coreldraw erstellt und mit einer 2ten Ebene gleich die Instrumente hinterlegt. So hatte ich eine Bohrschablone und zugleich die Instrumente. Das Instrumentenbrett wird aus 1,5mm FzSph geschnitten und gebohrt. Anschließend wird der Pilz aus 3 Lagen 10 mm Balsaholz geformt und mit 1mm Balsa und 2 lagen 40er überzogen, gespachtelt, geschliffen und lackiert. Das Instrumenten Brett wird mit Ahorn Beize eingestrichen. So sieht meine Variante aus. Meine Mitbaukollegen sind auch nicht untätig und haben unterschiedliche Varianten gebaut.
Einbau des Motors. Zuerst bohren wir den Rumpf auf, dann bauen wir wieder ein Muster für den Motorspant. Der Motor soll einen Sturz von mindestens 6° erhalten und etwas Seitenzug. Wir bringen den Rumpf anhand der Wurzelrippenmitte in die 0 Grad Position und passen dann den Spant entsprechend an. Der Muster Spant passt. Jetzt kann der Spant aus 2mm GFK hergestellt werden. Für den Einbau wird er noch etwas angepasst und schräg angeschliffen damit er besser in den Rumpf passt.
Roland hilft uns beim fixieren des Spants mit 2min Harz. Anschließend wird der Spant mit 24h Harz und Rovings verstärkt.
Die Schleppkupplung wird im vorderen Bereich montiert. In ein Hartholzklotz wird ein 4mm loch gebohrt und ein Bowdenzugrohr eingeklebt. Jetzt wird ein ca 10×4 mm Loch rausgefräst. Mit 24h Harz und ordentlich Vaseline wird der Klotz in den Rumpf geharzt. Das Servo wird auf Holzblöcken gelagert. Das Akkubrett wird aus 1,5mm FzSph geschnitten, damit wir es wieder rausziehen können um zu Servo und Regler zu kommen. Von Roland haben wir den Tip erhalten eine Taschenlampe auf den Schleppkupplungsklotz zu legen um den Ausschnitt des Rumpfes raus zu fräsen. Perfekt !!
Endlich die Flächen sind dran :-)… Zuerst schneiden wir die Störklappen aus. Die Querruder sind werkseitig schon angezeichnet allerdings gefällt uns das nicht ganz. Also Querruder neu anzeichnen und parallel dazu gleich die Ausschnitte für die Servokästen. Die Servokästen baue ich aus 4mm Sperrholz, Jürgen baut die Kästen in der nobleren Variante aus 2mm FzSph. Nachdem probesitzen der Servokästen werden diese dann wieder mit 24h Harz eingeklebt. Die Fläche wird anschließend komplett verschliffen und gespachtelt bevor die Querruder ausgeschnitten werden.
Die Querruder können nun ausgeschnitten werden. Dazu fixiere ich ein Stahllineal mit doppelseitigem Klebeband auf der Tragfläche um einen sauberen Schnitt herzustellen ohne dass das Lineal verrutscht. Anschließend werden die Flächen und Querruder verkastet.
Die Ruderhörner zeichne ich mit CorelDRAW. Diese werden dann aus 2mm GFK hergestellt. Angelenkt werden die Querruder mit Kugelköpfen.
Jetzt noch ein paar Stecker montieren, drüber schleifen und nochmal am Rumpf anstecken. Jop passt. An den Randbögen hab ich noch „Fischchen“ 🙂 aus 3mm FzSph gefertigt um die Enden beim Landen zu schützen. Diese werden mit 2mm Inbusschrauben gesichert.
So jetzt mal alle Komponenten zusammenstecken. Verdammt die B4 neigt sich Stark auf eine Seite. Ok, alles wieder auseinander und die Flächen wiegen. Siehe da die eine Fläche ist ca. 70g schwerer als die andere. Nach einigen Diskussionen im Club und Internet Recherche wie ich das Problem lösen könnte, hab ich mich entschlossen dies auf eine einfach Weise zu bewerkstelligen.Also alle Komponenten wieder ran und rein in den Rumpf. Dann den Rumpf am Heck aufliegen lassen und die Nasenspitze hochheben. Das Blei, also die Differenz der Flächen (70g), an der leichteren Fläche solange verschieben bis die B4 im Gleichgewicht ist.An dieser stelle wird die Fläche in der Nähe des Holms geöffnet. Ideal wäre natürlich im Schwerpunkt der Fläche. Ich verwende etwas weniger Blei ca. 55g da ja auch noch Harz reinkommt.Anschließend nochmal verschleifen und los kanns gehen mit der Foliererei.
So es geht dem Ende zu. Mit Aceton wird die ganze Fläche gereinigt. MERKE immer in eine Richtung ziehen sonst stehen die verdammten Fasern wieder auf 😉 .Wir verwenden Oracover Scaleweiß und Orastick Klebefolie fürs Dekor. Die Folie wird in zwei Hälften geschnitten für oben und unten. Beide Teile werden „gleichzeitig“ aufgebügelt. Die unteren Folie wird an der Nasenleiste angebügelt und anschließend mit der oberen Folie überlappt. Selbiges an der Endleiste. Zuerst wird die obere Folie auf der Unterseite angebügelt und im Anschluss die untere Folie vollständig aufgebracht.Nachdem die beiden Flächen fertig sind kann schon mal der erste Dekorstreifen rauf. In Seifenwasser getränkt wird der rote Streifen vorsichtig aufgebracht. Durch das Seifenwasser kann ich noch Korrekturen vornehmen. Gaaaaaanz Vorsichtig das Wasser mit nem Lumpen rausstreifen.
Anschanieren von Querruder und Höhenruder. Oh mann, nach diversen Forenbeiträgen und durchackern von Anleitungen versuchen wir halt mal mit Silikon. Hmmm dachte das verwendet man nur im Bad.Egal also zuerst mal ein kleines Brett als Testaufbau. Zuerst eine dicke Lage Abdeckband drauf um das Ruder stabil zu halten. Das Silikon wird von der Tube in die Spritze gefüllt und mit dieser dünn in den Spalt gefüllt. Zuvor hab ich mir ein Hölzchen erstellt und geschliffen um das Silikon abzuziehen. Der erste Versuch ging recht gut allerdings stört das transparente Silikon etwas. Beim 2ten Versuch hab ich Micro Ballons zuvor in den Spalt gekippt und auf das Klebeband gedrückt. Zum einen färbt sich das Silikon leicht und das Klebeband kann leichter abgezogen werden. Das Ergebnis ist perfekt und hält bombig. Leider gibt’s von der Herstellung keine Fotos.
Zum Schluss noch die Ruderhörner einharzen und die Anlenkung fertig stellen.
Sooo, Ende in Sicht, fehlt nur noch die Lackierung. Der Rumpf wird komplett verschliffen, gespachtelt und abgedeckt. Los geht’s mit der Lackierung. Der Rumpf wird weiß grundiert, die Nase Schwarz und der Rumpfboden Verkehrsrot lackiert. Vielen Dank an Erich und Norbert für Ihre Unterstützung.
Finish. Endspurt. Finale. Endlich fertig. Das Dekor wird noch fertig gestellt. Orastick Klebefolie.
Die ersten zwei Erbauer sind sichtlich stolz und haben erfolgreich Ihren Erstflug absolviert 🙂 . Nur die Kennung fehlt noch, die gibt’s aber erst am Hahnenmoos. Muss ja verdient werden 😉
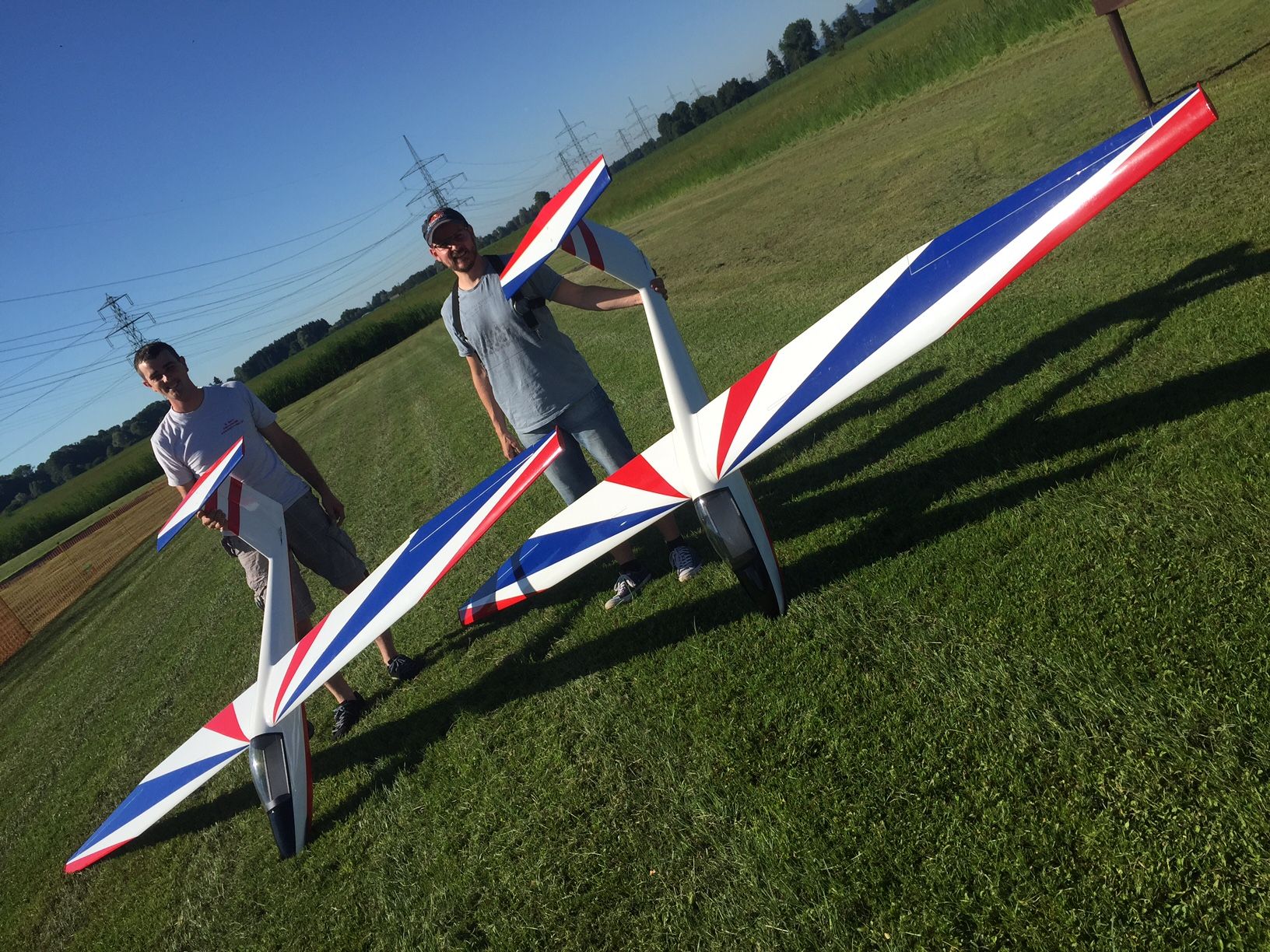
Ein kurzer Trimm da und dort und gut ist. Jetzt fehlen nur noch die fertigen B4’s von Roland und Jürgen. Also Jungs Gas geben.
Bei den nachfolgenden Einstellflügen konnten wir noch etwas Angstblei aus der Nase nehmen sowie die EWD anpassen.
Mit ca. ~5,5 – 6kg Gewicht ist sie nicht die leichteste hat aber ein guten Durchzug und fliegt wie auf Schienen. Jetzt fehlt nur noch ein Cockpit Ausbau, der muss allerdings noch etwas warten.
Die B4 durfte bereits Ihren Erstflug am Hahnenmoos absolvieren und ich bin nach wie vor begeistert. Ein Fixstarter für nächstes Jahr 😉
Inzwischen wird das nächste Projekt ebenfalls wieder von Rippin geplant. Ich für mich bin mit der Qualität des Bausatzes zufrieden. Eines muss natürlich jedem Bewusst sein, es ist kein ARF Modell, wer aber noch gerne selber baut und denkt 🙂 der ist mit dem Bausatz gut beraten. Für mich stimmt hier einfach das Preis Leistungsverhältnis. Zum Schluss noch eine kurz Anmerkung zur Lieferzeit. Rippin fertigt erst nach Eingang der Anzahlung bzw. Bestellung. Meist bestellen alle auf den Winter hin somit muss man mit längeren Lieferzeiten ~3-4 Monaten rechnen. Merke: Bestellen im Frühling 😉
Hinterlasse einen Kommentar
Du musst angemeldet sein, um einen Kommentar schreiben zu können.